Introduction: Polycrystalline diamond (PCD) saw blades have gained significant popularity in various industries due to their exceptional cutting capabilities and long lifespan. This article aims to provide an overview of the current usage trends and advancements in PCD saw blade technology.
- Increasing Demand: The demand for PCD saw blades has been steadily rising in recent years. This can be attributed to their ability to cut through a diverse range of materials, including wood, plastic, composite materials, and even non-ferrous metals. As industries continue to seek more efficient and precise cutting solutions, PCD saw blades have become indispensable tools.
- Enhanced Durability: One of the significant advantages of PCD saw blades is their remarkable durability. Unlike traditional saw blades, which may blunt after extended usage, PCD saw blades maintain their sharpness for a more extended period. The diamond particles embedded in the saw blade’s cutting edges provide exceptional resistance to wear, resulting in reduced downtime for blade changeovers and increased productivity.
- Improved Cutting Performance: PCD saw blades are characterized by their excellent cutting performance. Their superior design and precision-engineered tooth geometry allow for smooth and precise cuts, minimizing chipping and tear-out. This makes PCD saw blades ideal for applications where accuracy and surface finish are critical, such as in the manufacturing of furniture, flooring, and automotive parts.
- Versatile Applications: PCD saw blades are highly adaptable and find applications across various industries. They are commonly used in woodworking, where they excel in cutting hardwood, plywood, and laminates. Additionally, PCD saw blades have found their way into the plastic fabrication industry, enabling efficient and clean cutting of materials like PVC, acrylic, and polycarbonate. The ability to cut non-ferrous metals further expands the scope of their applications.
- Technological Advancements: Recent advancements in PCD saw blade technology have further enhanced their performance and versatility. Manufacturers have developed innovative bonding techniques, such as laser welding, to improve blade strength and stability. Additionally, advancements in PCD material composition have resulted in stronger and more wear-resistant saw blades, ensuring prolonged tool life and high cutting efficiency.
- Proper Maintenance and Care: While PCD saw blades are renowned for their durability, proper maintenance and care are essential to maximize their lifespan. Regular cleaning, lubrication, and storage in a controlled environment can prevent resin build-up and corrosion. Following manufacturer guidelines for usage and maintenance will ensure optimal blade performance and prolong the life of the PCD saw blade.
Conclusion: The current usage trends of PCD saw blades reflect their growing indispensability across various industries. As demands for higher precision and superior cutting performance continue to rise, PCD saw blades are rapidly becoming the preferred choice for professionals seeking efficient and reliable cutting solutions. With ongoing technological advancements, the future of PCD saw blades appears promising, promising increased versatility and improved cutting efficiency.
PCD saw blade brazing machine
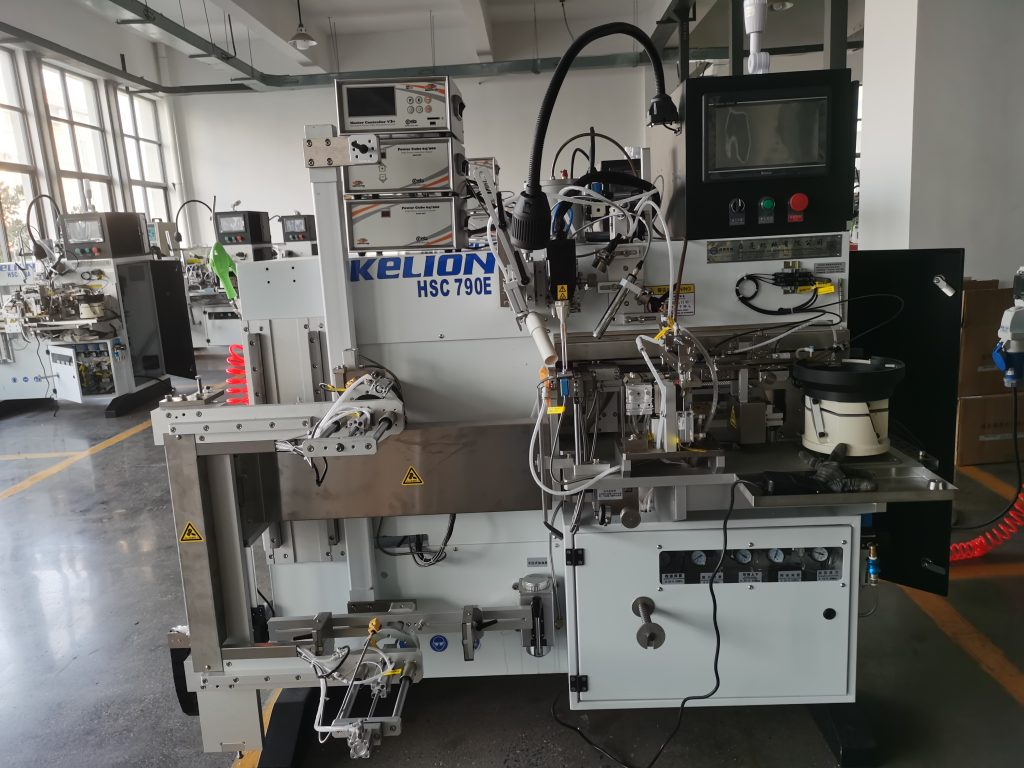